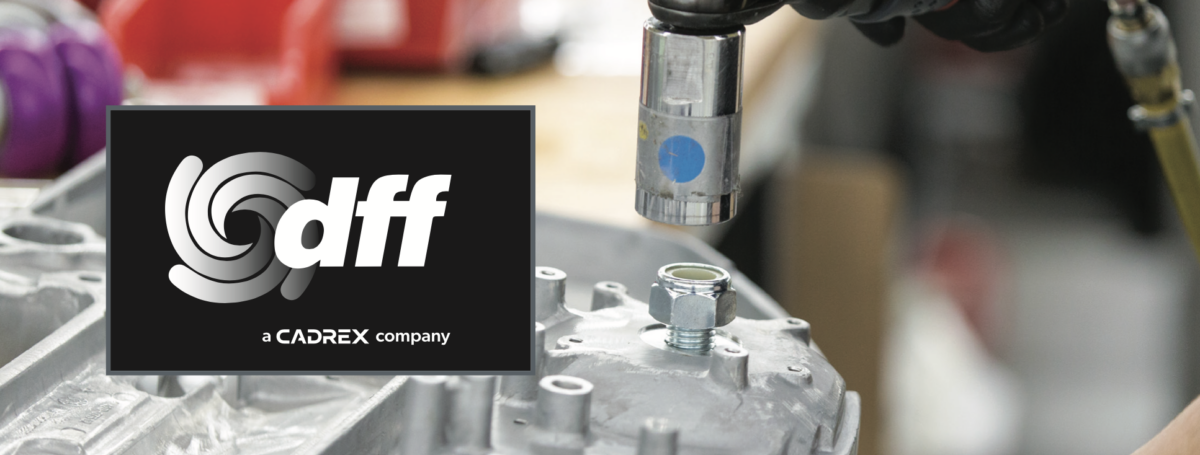
Times Have Changed
DFF, a CADREX company was founded in 1969, primarily producing low-volume prototype components. These prototype orders led to production orders and eventually to fully tested electro-mechanical assemblies. Today, DFF has grown into a contract manufacturer specializing in medium to high volume production of precision-machined components and electro-mechanical assembly products.
Company President William (Bill) Marganti began at DFF in the Quality Control department and possesses 38 years of hands-on experience. Our team of experts offers engineering design assistance including design for manufacturing (DFM), design for assembly (DFA), and geometric dimensioning and tolerancing (GD&T) enhancements. We added an additional 165 people to the team in 2021 for a total of 325 employees throughout DFF.
Despite our tremendous growth, we remain rooted in the belief that responsiveness to our customer needs will continue to separate us from our competition. Our facility began with a 2,000-square-foot building, but increased client demand quickly led to a need for more space and more capabilities. With a recent construction project, we added two buildings and increased our total square footage to 300,000.
This new area paved the way for new capabilities, including 30 large CNC machines, some of which are operated by robotic cells, to our existing fleet. We also recently invested in a digital Gemba Board to track the status of our workplace in real time. This tool has proven invaluable as an indicator of key factory metrics involving safety, quality, delivery, cost, and inventory. It provides detailed insights into any customer, project, or part, helping to streamline our efficiencies and forecast our projects.
What does DFF do for its customers?
To know more about DFF, it’s best to start with an understanding of what our name stands for: Defect Free Flow. This is the end goal of every project we undertake: to manufacture or assemble a product that is as near perfect as it can be. Our commitment to achieving defect-free products and the levels of quality assurance we provide are what sets us apart from our competition and allows us to maintain solid and long-lasting relationships with our customers.
Precision machining and manufacturing
At DFF, we’re known for our exceptional design-assist abilities and quality machining services. We leverage more than 100 CNC machines and boast extensive capacity to handle project runs of all sizes with a specialty in mid- to high-volume quantities.
Our capabilities are constantly evolving as we acquire new machinery and learn new processes to meet the growing needs of our client base. If projects require machinery we don’t have, we can invest in new equipment. Some of our customers benefit from the industrial robots we integrated into cells on our shop floor. In addition to allowing skilled employees to focus on other work, they increase productivity overall. Some have even lowered labor costs by as much as 90%.
Our capabilities include:
- 100+ CNC Machine Centers offering vertical, horizontal, and 5-Axis CNC machining services
- State-of-the-art robotic cells that improve productivity and lower costs
- Flexible machining system for low volume, high mix components. These systems include dedicated machines and pallet systems for a family of components
- CNC milling for prototyping and modeling of materials like metal or plastic
- CNC turning for mid- to high-volume runs of prototypes, spacers, shafts, or bushings below 2.5”
- An extensive tool room fully equipped with milling, lathe machines and more
- Real-time SPC (Statistical Process Controls) and drop or international shipments.
Thanks to our commitment to client satisfaction, our innovative technology, and our powerful CNC machinery, we are expertly poised to act as partners with our clients in their manufacturing endeavors. Our modern manufacturing area is climate controlled with 24/7 lights-out capability and the latest technologies.
Electromechanical assembly and test services
Customers looking for a partner to complete complex electro-mechanical assemblies or discrete orders, Kanban, or forecasts with releases, find what they need at DFF Corp. Our highly skilled technicians are capable of handling electromechanical assembly and test services, but more than that, our team ensures quality and reliability at a competitive price, right from the start of each project.
Our professionals have familiarity and expertise with the following:
- Building to customer BOM (Bill of Materials) and print requirements
- Following detailed work instructions
- Incorporating LEAN concepts
- Offering real-time SPC (Statistical Process Control)
- Meeting TUV/UL/CSA certification standards
- Offering ESD (Electrostatic Discharge) protection
- Performing drop or international shipments
- Meeting the needs of thermal product production
- Supply chain management
- Vapor degreasing
In addition, we offer the following specialized services:
- Torch brazing copper to copper tubing and fittings
- Nitrogen leak Detection: We offer pressure drop or air/underwater testing methods
- Hydrostatic leak detection to test pressure vessels for strength and leaks
- Helium leak detection, including both vacuum and pressure leak detection, performed to industry standards or customer specifications using custom tooling
- Hi-Pot/Ground continuity testing to industry standards or to meet customer requirements using customer-supplied connections. Hi-Pot testing is used for the insulation of components carrying electric current and ground continuity testing for any shorting of electrical components
We perform our services in-house in our spacious, clean, climate-controlled assembly area or in our testing area.
Engineering design assist
From development to production, our engineering design assist professionals are committed to helping our customers enhance the design of their part or part system.
The goal of our design-assist and design-build services is to ensure quality and reliability at a competitive price, right from the start. Our contract manufacturing facility operates 24/7 using the most advanced technology to meet this goal and to ensure client capacity needs are met.
- Design for Manufacturability (DFM)
- Design for Assembly (DFA)
- Additive Manufacturing
- Geometric Dimensioning and Tolerancing (GD+T)
- State-of-the-Art Engineering Software
- Continuous Process Improvement Activities
Quality planning services
We don’t just value quality in our own work, but also pride ourselves on assisting with quality planning for our clients. This speaks to our driving need and desire to solve problems and make manufacturing and operating easier and more productive for our customers. Some of our services include:
- Control plans
- FMEA (Failure Mode & Effect Analysis) services
- Gage R&R (Repeatability & Reproducibility)
- Process capability studies
- PPAP (Production Part Approval Process)
- Measurlink Real Time SPC (Statistical Process Control) software
- MiniTab SPC software
- Supply chain management
- Reach, RoHS, Conflict Minerals Compliance
What types of industries do you typically serve on a day-to-day business, and is there one you’d like to reach?
- Semiconductors
- Robotics
- Transportation and future technologies
- Business machines
- Medical Diagnostics
- Security imaging and detection
- Defense
- Warehouse and logistics handling
Any additional points you would like to tell potential buyers about? For example, what is the technology like at DFF?
- 130 CNC machines
- 2 robotic automation cells serving over 30 machines
- Flexible manufacturing systems
- VTL up to 24” diameter
- HTL up to 32” diameter
- Vertical and horizontal CNC up to 120”
Another thing that sets us apart from our competition is that we are a visual factory. The cornerstone of
this is our digital Fusion Gemba Board—designed by Datanomix—providing a real-time, automated indicator of safety, quality, delivery, cost, and inventory (SQDCI).
The board measures development at both strategic and tactical levels—tracking order progress, current performance, and our ability to hit both quality and delivery targets with consistency. Simply put, the board serves as the pulse of the factory, retrieving and sorting vital information to provide an overview of the operation. A dozen large TV screens around the production area and office suites allow everyone to see clear production indicators in real-time.
To supplement the board, our visual factory also consists of a clean and organized shop and quality assurance (QA) floor, visual instruction manuals for employees, and the use of CAD drawings for concept design work. All these elements add up to a living, breathing factory that’s consistently improving upon methods and practices to ensure on-time delivery, efficiency, and supply availability.
Prior to the visual factory, our production managers would walk the factory floor and work alongside operators to correct problems and make necessary changes to improve production speed and accuracy. Rapid growth and demand from new, global customers made this process unsustainable.
As the necessity for our services increased, we hired hundreds of new employees, deployed additional multi-million-dollar robotic machine cells, and increased our total square footage to 300,000. Now, with our new Fusion GEMBA technology, every square foot of our factory space is planned and documented to serve a purpose for our customers.
What DFF’s level of experience?
There are five major things that make DFF different from most other contract manufacturers:
1) Engineering design assist
Whether clients have a specific problem that needs to be solved or need a new perspective on a project, our engineering design assist services are second to none.
Our team carefully and thoughtfully evaluates the part or parts for manufacture, offering insight and suggestions for refinements that could both simplify the production process and reduce costs.
This is the very core of our business and what we really excel at. We love to get a challenging case and really knock it out of the park for our clients. We enjoy working closely with them to solve problems and find the best, most productive, and cost-effective solutions to every issue that comes our way.
2) Experience with tight tolerances
With extensive experience in the aerospace and defense industries, we’re no stranger to working within tight tolerances. For example, when a global defense company needed to design two 8-foot-long munition magazines for a newly designed, industry-leading weapon to be used on a fighter jet, they knew they could rely on us for the required precision, knowledge, and manufacturing equipment.
Our team didn’t disappoint—after significant design engineering, research, and development, we used our 3D printing technology to create a part to help conceptualize and facilitate roundtable discussions during the development phase. Then we manufactured two sets of prototype parts and sent them to the customer for testing, leading to a beta order and an ongoing partnership.
3) Electromechanical assembly capabilities
We are a partner that can assist with complex electromechanical assemblies to discrete orders, Kanban, or forecasts with releases. We frequently aid our clients within the transportation industry with component assembly for products associated with motor control. In addition, we help companies with technical needs get their products into the market. No matter the project, our team always ensures quality and reliability at a competitive price, right from the start.
4) Variable volume capacity
At our facility, we leverage more than 100 precision CNC machines and are capable of handling client projects of all sizes, with a specialty in higher-volume quantities. Our systems include two very large robotics lines, each with one robot that services at least 16 CNC machines by quickly moving large castings through the cell. We also invested in a digital Gemba board to measure our development at both strategic and tactical levels by tracking order progress and our ability to consistently hit both quality and delivery targets. These combined elements mean we are prepared to accommodate any high-volume orders.
5) Commitment to American manufacturing
Our team and our facility are both constantly growing and improving, while simultaneously remaining true to our commitment to American manufacturing, as we have since 1969. The majority of our work is conducted on our campus in Agawam, Massachusetts, or performed by one of our trusted suppliers. Through the efforts of our team and network, we’re able to keep costs down without having to resort to moving all production offshore.
Are you QS certified? Do you offer SPC? Any certifications DFF has received?
- AS9100 and ISO 9001 (DFF Certificate of Registration)
- EICC Member (Social and Environmental Policy)
- EANE Member
- National Safety Council Member
- ITAR Registered
- AIM Member
Describe DFF’s Quality Control program.
Both our precision manufacturing capabilities and quality assurance procedures are second to none. Precision manufacturing (also called Industry 4.0.) is an umbrella term referring to a manufacturer’s process controls. We use our 6,500-square-foot temperature- and humidity-controlled quality lab with 18 coordinate measuring machines (CMM) to carefully achieve our clients’ critical dimensions with pinpoint accuracy.
The standards to which we hold ourselves are the same standards to which we hold our partner suppliers. To that end, our supplier quality policy reads:
All DFF Corp. suppliers are an integral part of our organization; therefore, DFF Corp. will cooperatively work with our suppliers to assure that their products meet the necessary standards to ensure customer satisfaction. We will place, whenever possible, the facilities of our company at the disposal of our suppliers to help them with any problems they may encounter in supplying materials to our specifications and to aid them in developing better means for production and quality improvement.
We have established a goal of 10,000 PPM (parts-per- million) for all our suppliers. To ensure this goal is met, reports are calculated and shared with our suppliers. Any challenges that a supplier may experience are managed aggressively to help in their success.
What one thing would you like prospective customers to know about DFF?
We are continuing to hire and expand, including adding to our facility size. We offer great training to our already skilled workforce and look forward to continuing to bring more people on. With the help of our digital Gemba board and visual factory mindset, we are able to boost production and better understand our machines and operators. This has led to great success for us in the past two years through some of the most difficult times in many industries.
DFF
59 Gen Creighton W Abrams Drive
Agawam, MA 01001
Phone: 413-786-8880 www.dffcorp.com
President: William (Bill) Marganti
Sales Manager or Sales Contact(s): Keith Campbell, kcampbell@dffcorp.com